Konstruktionsrichtlinien für den 3D-Druck (FDM)
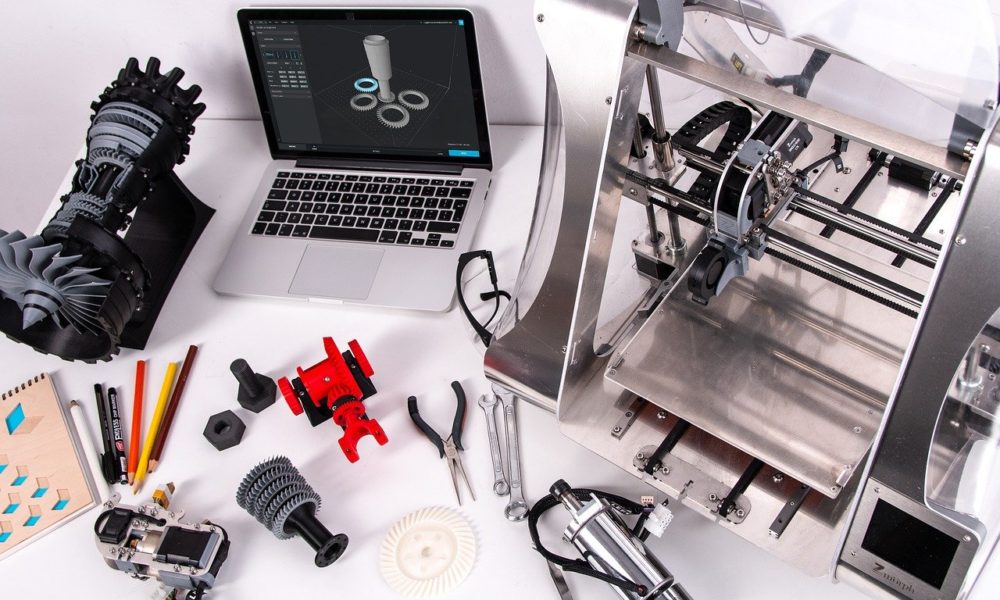
Die Konstruktion von 3D-Modellen mit anschließendem 3D-Druck kann heute theoretisch jeder relativ kostengünstig auch zu Hause durchführen. Die Beachtung einiger wichtiger Konstruktionsrichtlinien im 3D-Druck ist für das Erzielen von guten Ergebnissen unerlässlich. Ich habe daher einen Leitfaden für den FDM bzw. FFF-Druck zusammengestellt, und meine eigenen Erfahrungen aus mehreren Jahren 3D-Druck-Konstruktion einfließen lassen.
Es werden die Grundlagen der Konstruktion und fortgeschrittenes Konstruieren für den 3D-Druck unterschieden. Bei den Grundlagen liegt der Schwerpunkt in der fertigungsgerechten Konstruktion. Ziel dabei ist ein möglichst gut druckbares Bauteil zu konstruieren. Bei den fortgeschrittenen Tipps findet die spätere Funktionalität des Bauteils Berücksichtigung.
Der Artikel wird fortlaufend aktualisiert. Falls du Anregungen oder weitere Tipps hast, kontaktiere mich gern oder nutze die Kommentarfunktion. Ich nehme sehr gern weitere Tipps und Tricks im Artikel auf.
Inhaltsverzeichnis
Die grundlegenden Konstruktionsrichtlinien für den 3D-Druck (FDM)
Bereits im Konstruktionsprozess muss das 3D-Druckverfahren beachtet werden. Die Grundlagen zielen darauf ab, dass das Bauteil überhaupt druckbar ist und zudem möglichst gute Druckergebnisse erzielt werden. Daher sollten die folgenden Konstruktionsrichtlinien eingehalten werden.
1. Toleranzen beachten
Es sollten immer die Toleranzen des Druckers beachtet werden. Natürlich sind die genauen Toleranzen vor allem von der Qualität des 3D-Druckers abhängig. Als grobe Faustregel kann von einer Toleranz von ca. +- 0.5% ausgegangen werden. Ein Längenmaß von 100mm hat somit eine Genauigkeit von 100 +-0.5mm.
2. Wandstärken
Grundsätzlich sollten Wandstärken mindestens 1.5mm dick sein. Ausreichende Stabilität ist ab einer Wandstärke von 3mm gegeben. Es bleibt außerdem zu beachten, dass die Wandstärke immer ein Vielfaches des Düsendurchmessers sein sollte. Bei einer 0.4mm starken Düse sind also Wandstärken von 1.2, 1.6, 2.0mm usw. möglich.
3. Konstruktion von Bohrungen
Der Mindestdurchmesser der Bohrung liegt bei ca. 2mm. Kleinere Bohrungen sollten angedeutet und nach dem Druck erst aufgebohrt werden. Die Bohrungen sollten 0.1-0.75mm größer ausgeführt werden als eigentlich notwendig. Sind sehr genaue Ergebnisse gefordert, sollte der entsprechende Wert durch Testdrucke bestimmt werden. Vertikale Achslöcher sind aufgrund der Kompression des Schichtaufbaus ebenfalls als kritisch zu betrachten. Ist bei diesen Löchern eine hohe Genauigkeit gefordert, macht es Sinn die Bohrungen erst nachträglich einzubringen.
4. Erhabene und eingelassene Flächen
Die Richtlinien hier sind relativ einfach: Eingelassene Flächen sollten eine Tiefe und auch Breite von mindestens 1mm haben. Bei erhabenen Flächen sollte die Höhe ebenfalls 1mm sein. Die entstehende Wandstärke dagegen mindestens 1.5mm. Bei der Verwendung von Schriften ist darauf zu achten, dass nur Schriften ohne Serifen Verwendung finden.
5. Überhänge
Durch das Drucken von Schicht auf Schicht sollten nur bestimmte Wandschrägen bzw. Überhänge gedruckt werden, um ein möglichst gutes und stabiles Ergebnis zu erreichen. Als Regel gilt hier: Seitenflächen sollten zum Druckbett immer einen Winkel von über 45° aufweisen. Bei 45° wird die neu gedruckte Schicht von 50% der unteren Schicht gehalten, was noch ein gutes und stabiles Druckergebnis liefert. Das 3D-Modell muss also dementsprechend anders ausgerichtet, oder konstruktive Änderungen vorgenommen werden. Es sollte also während der Konstruktion bereits überlegt werden, wie das Bauteil auf dem Druckbett positioniert wird.
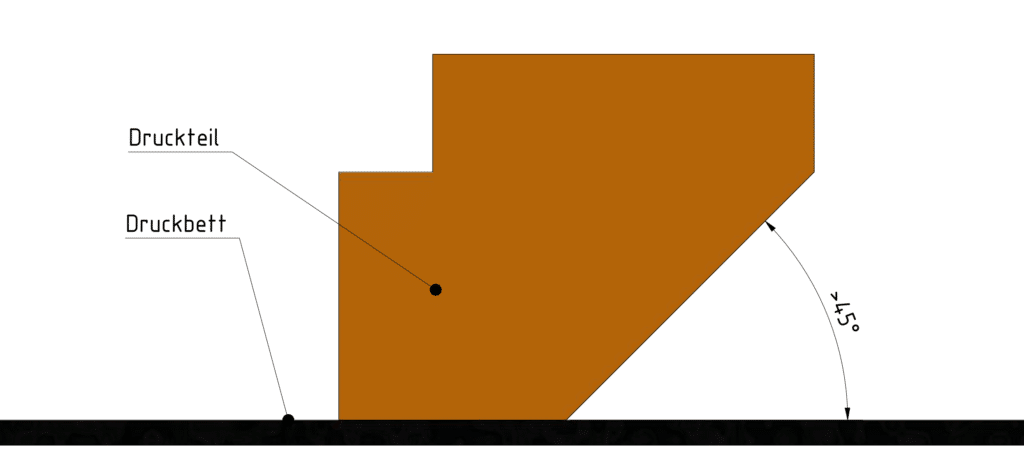
6. Supportstrukturen
Grundsätzlich sind Supportstrukturen wenn möglich zu vermeiden.
Dafür gibt es mehrere Gründe:
- die Druckzeit verlängert sich
- es kommt zur Materialverschwendung
- die Ergebnisse der Oberfläche sind nicht optimal
- es bedarf in der Regel einer Nachbearbeitung
Die Konstruktion sollte daher möglichst so angepasst werden, dass keine Supportstrukturen notwendig sind. Alternativ kann ein Bauteil auch getrennt und nach dem Druck zusammengeklebt werden. Hier werden in der Regel oft bessere Ergebnisse erzielt. Nur in Fällen wo es keine Alternativen gibt, ist der Einsatz von Supportstrukturen sinnvoll.
7. Brücken bzw. „Bridging“
Unter Bridging versteht man das Drucken in der Luft zwischen zwei Wänden. Der Name stammt vom veranschaulichten Beispiel des Brückenpfeilers. Durch sehr schnelle Bewegung des Druckkopfes kann so auch eine Brücke ohne den Einsatz von Supportstrukturen durch Drucken in der Luft realisiert werden. Allerdings nur in einem gewissen Rahmen. Bis zu einer Überbrückung von 5mm sind die Ergebnisse sehr gut, anschließend wird die Oberflächenqualität schon deutlich schlechter. Überbrückungen von über 10mm sollten vermieden werden.
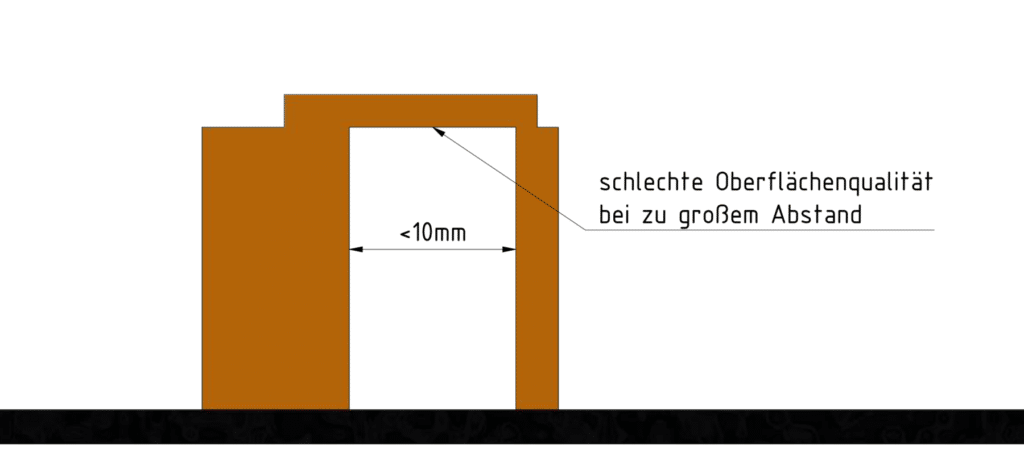
8. Bauteilverzug berücksichtigen
Die ungleichmäßige Verfestigung von Bauteilschichten führt zu unterschiedlichen Temperaturen im Bauteil und in der Folge zu Spannungen und Verzug. Um diesen Einfluss zu minimieren sollten lange und flächige Strukturen eher aufrecht gedruckt werden.
9. Kontakt zum Druckbett
Bei einer zu geringen oder sehr kleinen Kontaktfläche zum Druckbett sinkt die Bauteilstabilität mit zunehmender Höhe – die Ergebnisse können ungenau werden. Abhilfe kann hier eine geänderte Druckausrichtung schaffen. Durch die Bewegung des Druckbettes schwingt das Bauteil und folglich sinkt die Qualität mit zunehmender Höhe ab. Wie stark dieser Effekt ist, hängt natürlich von vielen Faktoren ab. So kann die Druckgeschwindigkeit reduziert werden, um hier schon ein deutlich besseres Ergebnis zu erzielen. 3D-Drucker mit stehendem Bett haben das Problem in der Regel nicht bzw. erst wenn das Bauteil an sich instabil wird.
10. Vermeidung von Elefantenfüßen
Die Düse komprimiert beim Drucken jeder Schicht das Druckmaterial nach unten, um eine möglichst gute Haftung zu erzielen. Die erste Schicht wird folglich breiter gedruckt als im 3D-Modell vorgesehen. Das Überstehen des Materials in der ersten Schicht zu den Schichten darüber wird als “Elefantenfuß” bezeichnet. Muss das Objekt anschließend irgendwo passend eingebaut werden, ist das Entfernen der Elefantenfüße unerlässlich. Alternativ kann eine Fase an das Bauteil angebracht werden. Dadurch entstehen bei richtiger Dimensionierung der Fase keine überstehenden Bereiche und das Bauteil kann ohne Nachbearbeitung eingebaut werden. Oft reicht hier schon eine 1.5mm Fase zur Vermeidung der Elefantenfüße aus.
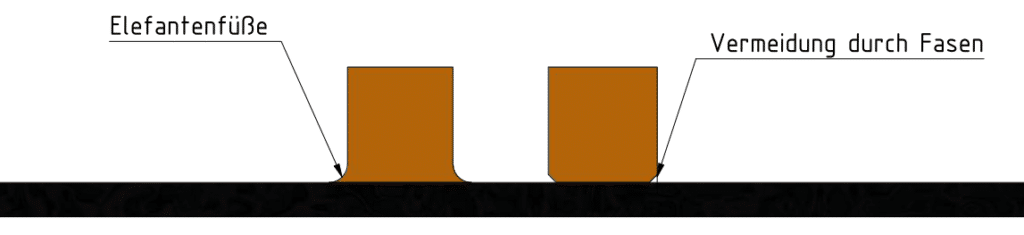
11. Export der CAD-Daten
In der Regel wird aus dem jeweiligen CAD-Programm eine STL-Datei exportiert. Diese Datei sollte mit möglichst hoher Auflösung exportiert werden. Gerade beim Einsatz von Bohrungen und Rundungen ist die hohe Auflösung notwendig, um ein gutes Druckergebnis zu erzielen. Bei dem exportieren Modell muss es sich um ein geschlossenes Solid-Modell oder um ein wasserdichtes Volumenmodell handeln.
12. Wahl der Schichthöhe
Für das finale Druckergebnis ist die Einstellung der Schichthöhe von großer Bedeutung. Je größer die Schichthöhe, desto schneller ist die Druckzeit. Allerdings sinkt dabei die Qualität der Oberfläche. Als guter Kompromiss hat sich hier eine Schichthöhe (Layerhöhe) von 0.2mm erwiesen.
13. Richtige Kompromisse finden
Die genannten Regeln stehen manchmal in Konflikt zueinander. Um Bauteilverzug zu vermeiden, druckt man ein Objekt aufrecht und geht damit das Risiko eines schlechten Kontaktes zum Druckbett ein. Mit der Erfahrung und der Priorisierung von Bauteileigenschaften lassen sich solche Konflikte jedoch auflösen.
Fortgeschrittene Konstruktionsrichtlinien von 3D-Druck Bauteilen
Die fortgeschrittenen Regeln gehen auf die spätere Funktionalität des Bauteils ein. Diese Grundregeln können nicht ganz so einfach wie die Grundregeln umgesetzt werden. Es ist ein wenig Erfahrung notwendig. Allerdings spielen meiner Ansicht nach gerade diese Konstruktionsregeln die Vorteile beim 3D-Druck erst richtig aus. Und das Konstruieren nach diesen Funktionsprinzipen kann auch viel Spaß machen.
1. Belastungsgerechte Schichtausrichtung beim FDM-Druck
3D-Druck hergestellte Bauteile mittels FDM-Verfahren sind aufgrund der Schichtorientierung in den unterschiedlichen Richtungen auch unterschiedlich belastbar. Es liegt also ein anisotropes Werkstoffverhalten vor.
Die spätere Belastung des Bauteils sollte im Vorfeld möglichst genau bekannt sein. Für reine Druckbelastungen ist die Schichtausrichtung nicht von Relevanz, für Zug- und Biegebelastungen jedoch schon. In der nachfolgenden Grafik sind die Belastungsrichtungen für Zug- und Biegebelastung in Abhängigkeit von der Schichtorientierung und die entsprechende Belastbarkeit dargestellt. Konkret lässt sich hier feststellen, dass eine Zugbelastung in z-Richtung (senkrecht zum Druckbett) möglichst vermieden werden sollte.
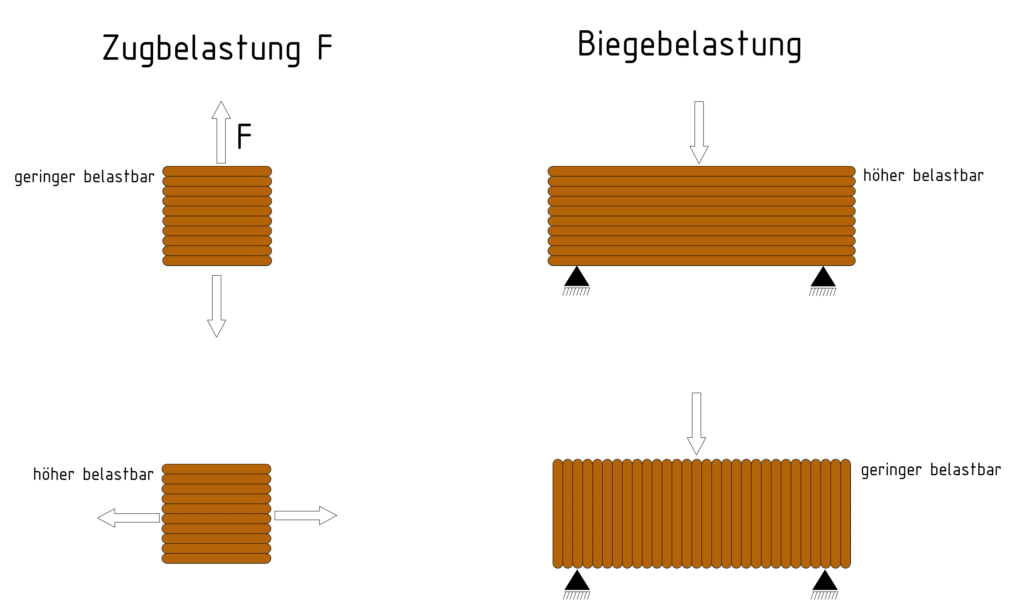
Für ein vertieftes Verständnis lässt sich die Ursache der geringen Zugfestigkeit senkrecht zur Schichtausrichtung auch anschaulich erklären. Durch den Schichtenaufbau des FDM-Druckverfahrens entstehen an den Rändern des Bauteils keine glatten Wände sondern Radien und dadurch sogenannte Kerben. Wird nun eine Zugbelastung senkrecht zur Schichtausrichtung beaufschlagt, so kommt es in den Kerben zur Spannungskonzentration. Die überhöhten Spannungen können einen Mikroriss zur Folge haben, der sich dann bei weiterer Lasterhöhung oder schwellender Belastung weiter ausbreitet und am Ende zum Versagen des Bauteils führt. Daneben sind die übereinanderliegenden Schichten nicht durch eine durchgängige Materialbahn gekennzeichnet, sodass bei nicht optimal verschmelzenden Schichten die Rissgefahr schon deutlich erhöht ist.
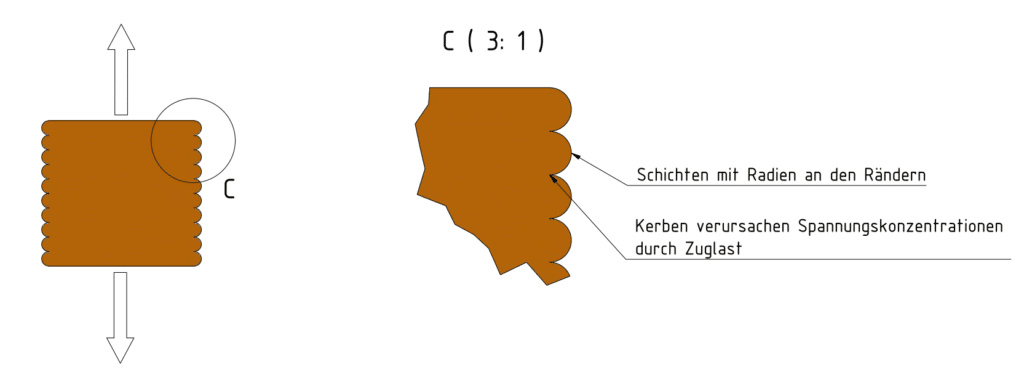
2. Radien und Rundungen anstatt scharfe Kanten
Eine der wichtigsten Konstruktionsrichtlinien beim 3D-Druck lautet: Trennung von jeglichen Gedanken und Erfahrungen aus konventionellen Fertigungsverfahren. Ein optimal ausgelegtes Bauteil ist in der Regel mit konventionellen Fertigungsverfahren nicht oder nur mit sehr hohem Aufwand fertigbar.
Daher gilt: Radien und Rundungen anstatt scharfe Kanten. Nicht in rechteckigen und viereckigen Bauklotzstrukturen denken, sondern das Bauteil wie Knetmasse betrachten. Scharfe Kanten, Ecken und Winkel verursachen in der Regel immer Spannungserhöhungen. Durch den Einsatz von Rundungen können die Spannungsspitzen reduziert und der Spannungsfluss im Bauteil besser abgeleitet werden. Die Rundungsfunktion im CAD-Programm ist also ein sehr oft eingesetztes Werkzeug.
3. Gewichtsoptimierung
Mit Hilfe des 3D-Druckes stehen in der Gewichtsreduzierung ganz neue Möglichkeiten bereit. Die Konstruktion kann dann so umgestaltet werden, dass überschüssige Materialanhäufungen entfernt werden. Konkret kann bei Kenntnis der Bauteilbelastung das Material dort reduziert werden, wo es nicht benötigt wird. Weiterhin können Leichtbauprinzipien und beispielsweise Wabenstrukturen oder die Sandwichbauweise eingesetzt werden.
Beim FDM-Druck ist ein weiterer wichtiger Parameter für die Gewichtsoptimierung die gedruckte Dichte des Innenraumes (engl.: Infill density). Vereinfacht kann sich hier an folgenden Werten orientiert werden:
- 0-15% Innenraumdichte: Für Dekorationsobjekte ohne weitere Funktionen
- 15-50% Innenraumdichte: Die am weitesten verbreitete Innenraumdichte liegt bei ca. 25%. Ein guter Kompromiss zwischen Festigkeit, Materialverbrauch und Druckzeit
- 50-100% Innenraumdichte: Für Objekte mit mechanischer Funktion und Anforderungen an Festigkeit ist in der Regel eine höhere Innenraumdichte notwendig. Die Objekte sind deutlich robuster bei höherem Materialverbrauch und höherer Druckzeit
Es wird an dieser Stelle schon ersichtlich, dass Erfahrungswerte hier eine immer größere Rolle spielen. Die Funktion des Bauteils und die damit verbundenen Belastungen sollten möglichst genau bekannt sein.
4. Einsatz der Formoptimierung (Bionik)
Aufbauend auf die vorangehenden beiden Punkte ist die Formoptimierung von Bauteilen sicherlich die komplexeste Art der konstruktiven Gestaltung von Bauteilen. Hier ist eine genaue Kenntnis der Bauteilbelastung Voraussetzung. Das Thema ist sehr umfangreich und wird im Blog noch in weiteren Beiträgen behandelt werden.
Es stehen heute Simulationsprogramme zur Verfügung, welche die Spannungen im Bauteil genau berechnen, auswerten und optimieren können (FEM-Finite Elemente Methode). Privatanwender können hier auch auf kostenlose Open Source Anwendungen zurückgreifen. Die FEM-Verfahren sind sehr genau aber auch aufwändig.
Durch einfache Hilfsmittel kann eine Kraftverlaufsanalyse durchgeführt werden. Prof. Dr. Claus Mattheck hat mehrere Bücher zum Thema veröffentlicht und beschreibt sehr verständlich und mit einfachen Methoden die „Körpersprache der Bauteile“. Er nimmt die Natur als Vorlage und leitet daraus geeignete „Denkwerkzeuge“ für technische Bauteile ab. In der Natur zeigt sich die perfekt angepasste Form, und mittels Beobachtungen kann diese in die eigene Konstruktion übernommen werden. Ich empfehle Jedem der sich in dieser Richtung weiterbilden möchte das Buch „Denkwerkzeuge nach der Natur“ von Claus Mattheck*. Mir hat es sehr geholfen ein besseres Verständnis zu erlangen und zudem mit einfachen Methoden schnell zum Ziel zu gelangen. Eine dabei beschriebene Methode zur Formoptimierung ist der Einsatz von Zugdreiecken. Diese Methode kann meiner Meinung nach oft eingesetzt werden und daher möchte ich Sie hier kurz erläutern.
Die Methode der Zugdreiecke
In der Natur sind optimal ausgelegte Radien zur Belastungsreduktion eher selten. Es existiert vielmehr ein Bild von individuell abgerundeten Ecken. Prof. Mattheck bringt hier die Methode der Zugdreiecke ins Spiel. Dabei soll die rechtwinklige Kerbe eines Bauteils, welche unter Zugbelastung steht, spannungsoptimiert werden. Die rechtwinklige Kerbe verursacht sehr hohe Spannungsspitzen -an dieser Stelle kommt es bei zu hoher Zugbelastung zum Bauteilversagen.
Durch die Methode der Zugdreiecke wird eine individuell abgerundete Form erstellt (siehe nachfolgende Grafik). Diese Vorgehensweise lässt sich relativ einfach nachbilden und sorgt für eine deutliche Reduktion der Spannung. Im Mittel erreichten die mittels Zugdreieck optimierten Proben im Vergleich zum normalen Radius bei gleicher Lastamplitude eine ca. 10-fach höhere Lastwechselzahl bis zum Versagen. Das ist wirklich sehr erstaunlich. Gerade bei Bauteilen für den 3D-Druck ist diese Methode aus meiner Sicht äußerst vorteilhaft. Die kritischen Zugspannungen können so deutlich reduziert werden. Gleichzeitig ist die Umsetzung relativ einfach und für den 3D-Drucker perfekt zu fertigen.
Übrigens treten die Zugdreiecke in der Natur ständig auf. Die Form eines Baumstammes ist nahezu identisch zum Zugdreieck. Auch bei senkrecht gespreizten Daumen zu Zeigefinger zeigt sich in der Hand das Zugdreieck.
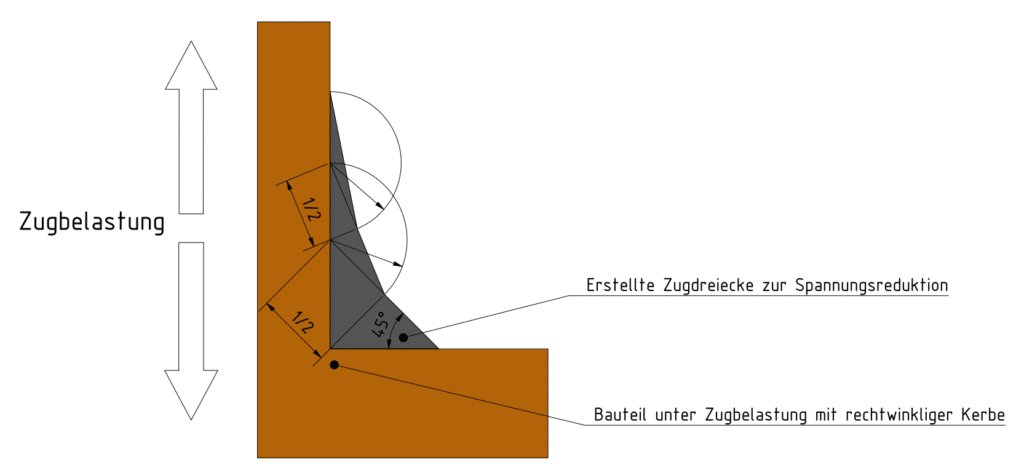
Zusammenfassung
Der Artikel beschreibt die wichtigsten Konstruktionsrichtlinien für den 3D-Druck.
Im ersten Teil werden die Grundlagen behandelt, welche die fertigungsgerechte Konstruktion in den Mittelpunkt stellen. Diese Konstruktionsregeln können sehr schnell umgesetzt werden.
Im zweiten Abschnitt zur fortgeschrittenen Konstruktion von 3D-Druck Bauteilen steht das Funktionsprinzip und die Belastung im Vordergrund. Hier wird mehr Erfahrung benötigt, allerdings zeigt das Beispiel der Zugdreiecke sehr schön, wie trotzdem schnell zu einem tollen Ergebnis gelangt werden kann.
Der Artikel beschreibt die einzelnen Punkte zum Teil recht ausführlich. Daher habe ich eine Zusammenfassung des Artikels erstellt. Diese kann mit Klick auf den nachfolgenden Button heruntergeladen werden. Somit kann sich jeder die wichtigsten Punkte ausdrucken und bei der nächsten Konstruktion an seine Seite legen. Viel Erfolg damit! 🙂
Bleibe auf dem Laufenden und erhalte wichtige News der Konstruktionsbude!
*Hinweis zu den Produktlinks:
Bei Produktlinks, die mit einem Sternchen(*) gekennzeichnet sind, handelt es sich um sogenannte Affiliate-Links. Wenn du auf einen dieser Links klickst und etwas kaufst, bekomme ich eine kleine Provision, ohne dass es dadurch für dich teurer wird.
Ich empfehle dir ein Produkt nur dann, wenn es mich wirklich überzeugt hat und nicht weil ich für deinen Kauf eventuell eine Provision erhalte.
4 Comments
Die Wandstärke sollte von der Extrusionsbreite abhängig sein oder? Die ist irgendwo bei 0.5x bei 0.4er Düse.
Hallo Carsten,
vielen Dank für dein Kommentar. Ja, da hast du recht. Bei mir entspricht in der Regel immer die Extrusionsbreite dem Düsendurchmesser. Ich ändere meist nur die FlowRate, wenn ich mit dem Ergebnis nicht zufrieden bin.
Wird im jeweiligen Slicer-Programm allerdings die Extrusionsbreite abweichend vom Düsendurchmesser eingestellt, so interessiert das Programm sich bei der Erstellung des Fahrweges nicht mehr für den Düsendurchmesser. Somit liegst du richtig und die Wandstärke muss dann ein Vielfaches der Extrusionsbreite sein. In der Regel werden für die Extrusionsbreite Werte von 100%-140% des Düsendurchmessers als sinnvoll angesetzt.
Danke für dein Feedback! Ich werde den Artikel bei Gelegenheit updaten und dein Kommentar auch einfließen lassen.
Viele Grüße!
Die 45° -Regel gilt meiner Ansicht nach nur bei Überhängen für Schichtdicken = 0,5 x Extrusionsbreite.
Ich selber drucke oft mit einer 1mm Düse. Da kann ich dann bei einer Schichtdicke von 0,2mm problemlos 20° Schrägen drucken. Auch bei einer 0,4mm Düse müßten bei einer Schichtdicke von 0,1mm problemlos 30° drin sein.
Hallo Roger,
danke für deinen Hinweis.
Mit 45° ist man in der Regel immer auf der sicheren Seite.
Durch Testen kann hier sicherlich immer noch ein wenig optimiert werden!
Viele Grüße und Spaß bei deinen Projekten!